
Adamastream Raw Material
Adamastream excels in the production of exceptionally precise industrial components crafted from hard materials such as synthetic ruby, synthetic sapphire, ceramics, and carbide. As a foremost manufacturer, they specialize in these durable materials to ensure top quality and performance in demanding industrial applications.




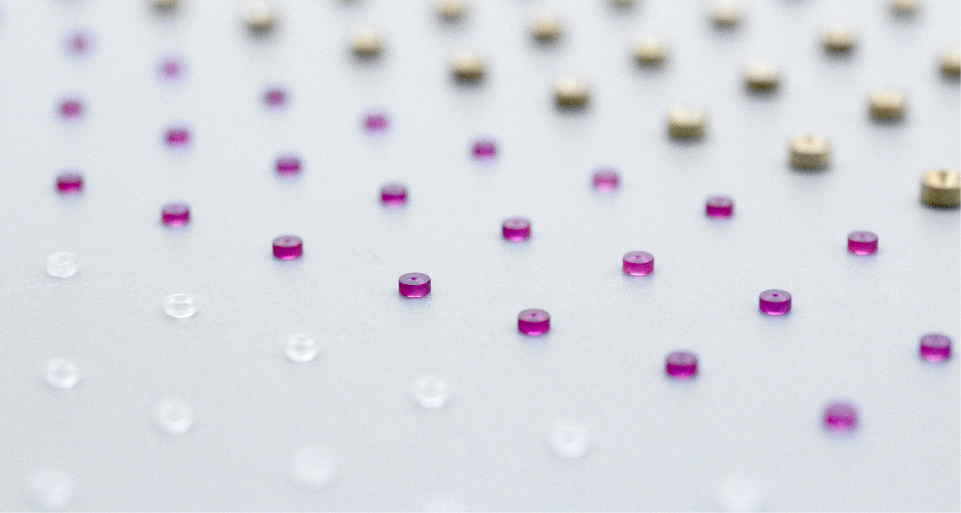
The Dual Identity of Ruby and Sapphire
Corundum, the second hardest natural mineral, is known as ruby when red and sapphire in other colors. Both gemstones are highly durable and scratch-resistant, making them suitable for various applications. Despite their identical composition, rubies contain trace amounts of chromium, giving them their red color, while different internal structures are created during manufacturing. End users often do not realize that these gemstones are composed of the same material.
Characteristics
Physical and Mechanical Properties
Properties | Unit | Value |
Structure | / | Single Crystal |
Chemical Formula | / | Al2O3 |
Index of refraction | / | No: 1.768 (c-axis)Ne: 1.760 (c-axis) |
Infrared of penetrable index | % | >85 |
Specific Gravity | g/cm3 | 3.97 |
Theoretical Density | % | 99.98 |
Hardness | Mohs | 9 |
Tensile Strength | GPa | 0.19 |
Compressive Strength | GPa | 2.1 |
Flexural Strength | GPa | 340~380 |
Dielectric Constant | 11.5 parallel to C-axis9.3 perpendicular to C-axis | |
Dielectric Strength | V/cm | 48000 |
Melting Point | °C | 2000 |
Coefficient of Expansion | °C | 4.3 x 10-6/°C (perpendicular to C-axis)5.4 x 10-6/°C (parallel to C-axis) |
Specific Heat | J/kg.°C | 750 |
Learn More
About
Adamastream
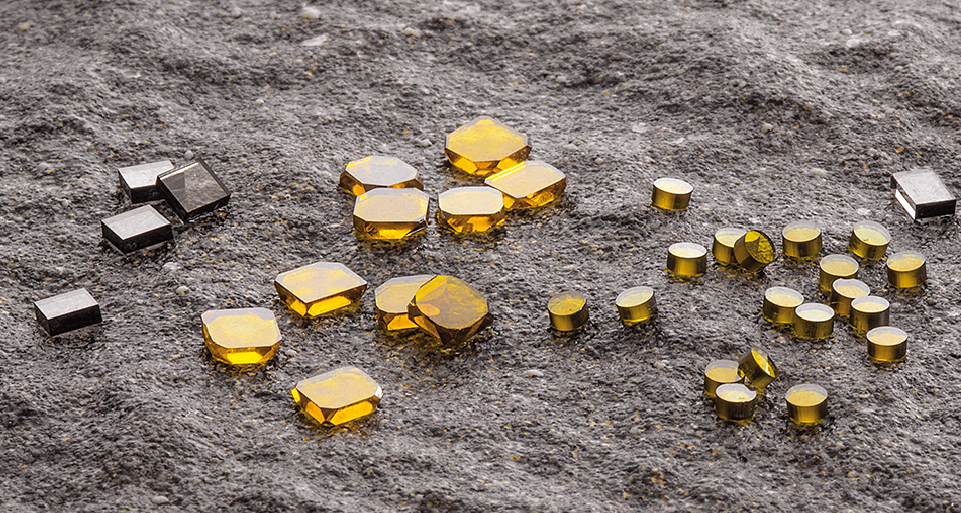
The Ultimate Hardness Champion on the Mohs Scale
Diamonds hold the highest score on the Mohs hardness scale, consisting of superior quality single crystal diamond. This makes them the hardest material known to exist on Earth. Interestingly, the perfect score of 10.0 on the Mohs scale signifies not merely a single point advancement over ruby but represents an exponential increase, emphasizing the non-linear nature of the scale.
Methods of Diamond Formation
Learn More
About
Adamastream
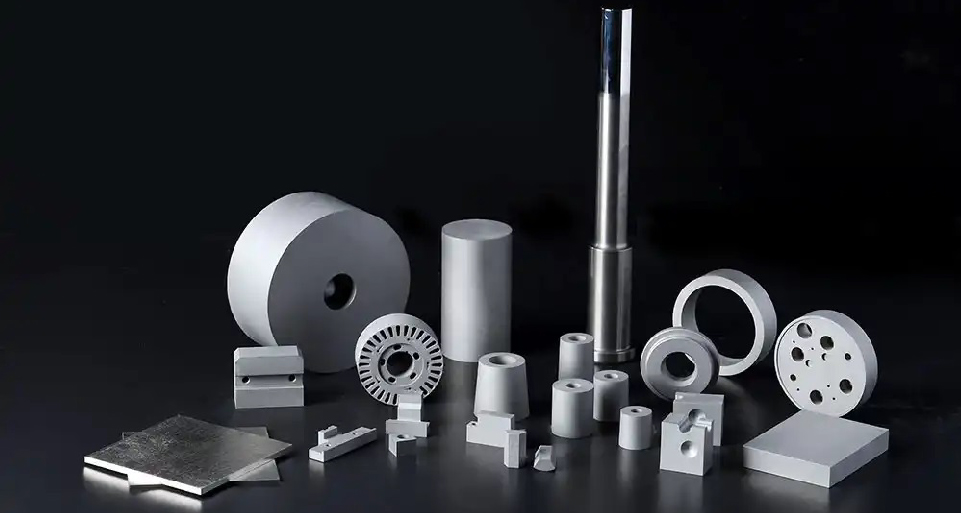
The Pinnacle of Hardness and Wear Resistance
Tungsten carbide, commonly referred to as cemented carbide, is a material known for its extreme hardness and excellent wear resistance. It is synthesized from tungsten and carbon through a powder metallurgy process. Tungsten carbide is widely used in cutting tools, drill bits, molds, and various wear-resistant equipment. Its main advantage is its ability to maintain stable performance under extreme working conditions such as high temperatures, high pressures, and high friction environments.
Characteristics
Structural and Hardness Properties
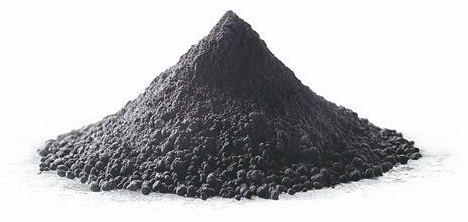
Material | Hardness | WC (Grain size) | Co | |
Structure | HRA | HV | µm | wt% |
WC-Co | ~95.6 | ~2550 | ~0.3 | 0.5 |
Tungsten carbide, due to its exceptional properties, is widely used in:
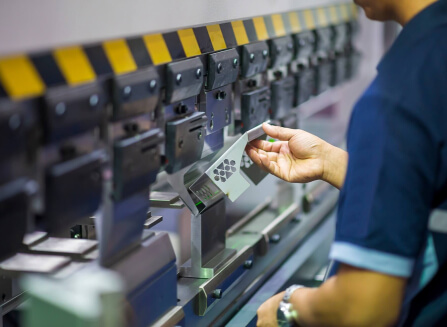
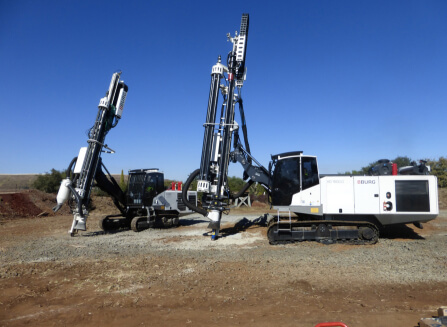
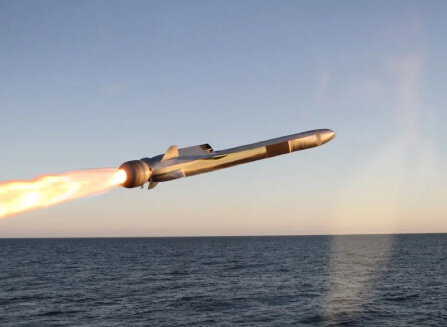
Learn More
About
Adamastream
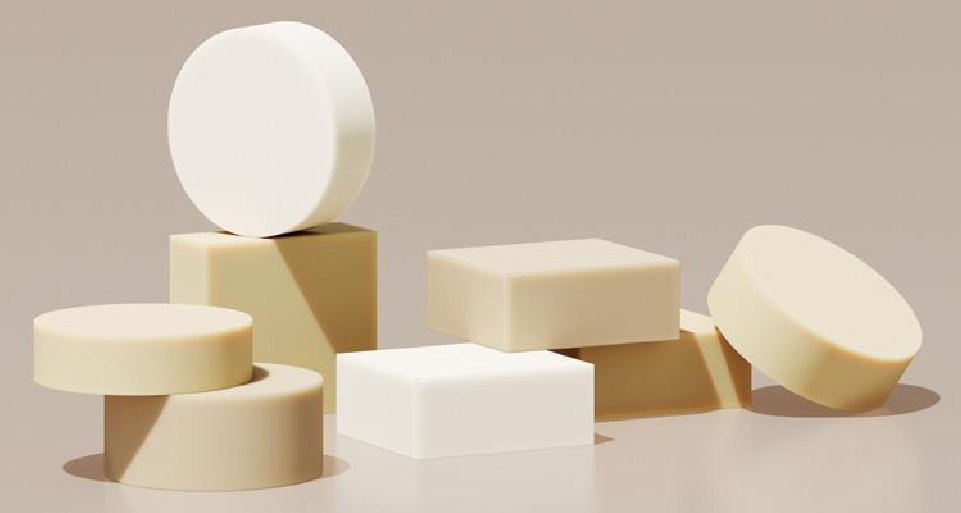
High Hardness and Heat Resistance
Ceramic materials are made from inorganic, non-metallic materials that are sintered at high temperatures. These materials typically exhibit high hardness, high melting points, excellent heat resistance, and good electrical insulation properties. In modern industry, the use of technical ceramics is increasingly widespread, including materials like alumina, silicon carbide, and silicon nitride.
Characteristics
Structural and Hardness Properties
Properties | Unit | Aluminia | Zirconia |
Structure | / | Poly | Poly |
Composition(wt %) | / | Al2O3 | ZrO2 |
Purity | % | 99.90 | 95 |
Density | g/cm3 | 3.90 | 6.00 |
Hardness | HV | 1900 | 1200 |
Compression strength | MPa | 2500 | 2000 |
Fusion Temperature | °C | 1500 | 1000 |
Thermal Expansion | 10%/K | 8.20 | 10.50 |
Chemical Resistence | (Acids) | Excellent | Good |
Chemical Resistence | (Bases) | Good | Good |
Ceramic materials are broadly used in areas such as:
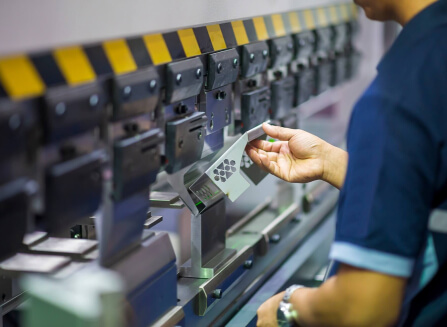
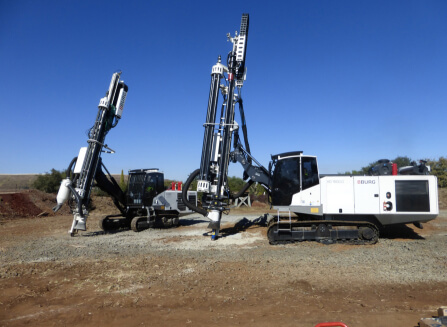
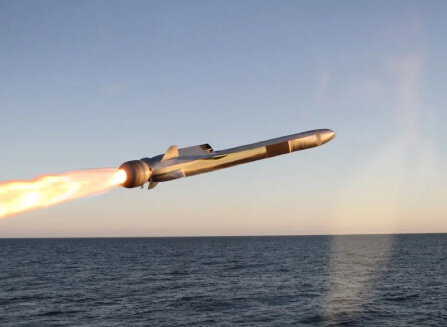